Le sensei entre dans l’usine et interroge : « Qu’est-ce que vous faites encore là ? Une usine d’injection plastique en Île de France ! Qu’est-ce que cela signifie de produire en France pour vous ? »
En ne comprenant pas vraiment la question du sensei, nous avons tenté de répondre :
« Eh bien … produire en France est signe de qualité dans le monde ! Nous avions aussi bénéficié de la position géographique de nos clients. Maintenant, cela n’est plus un argument.«
« Signe de qualité !? Sûrement pas ici ! Regardez donc votre atelier !«
Qu’est-ce qui crevait les yeux du sensei mais que nous ne parvenions pas à voir ?
Nous ne comprenions pas, nous avons fait beaucoup d’efforts sur la qualité, l’entreprise était, il y a de cela quelques années, classée parmi les plus mauvais fournisseurs et beaucoup de nos clients, des fournisseurs de rang 1 de l’automobile, refusaient de travailler avec nous. Tout comme certains constructeurs automobiles. Beaucoup d’efforts et d’énergie ont été déployés afin d’améliorer la situation de qualité de l’usine.
Et elle s’est améliorée, les réclamations clients ont grandement baissé, les clients levaient un à un leurs interdictions d’achat chez nous, le business était en croissance, ce qui nous démontrait en quelque sorte que nos clients nous faisaient confiance.
Ces résultats ont été obtenus en mettant en place un rituel hebdomadaire de suivi des réclamations clients, où l’équipe dirigeante de la production se réunissait pour prioriser les actions à la suite des réclamations et mettre en place des plans d’actions. En plus de cela ont été déployés les QRQC (Quick Response Quality Control) ainsi qu’une équipe de contrôle qualité en production qui ont permis aux experts de la qualité et de la production de repérer les défauts et de mettre en œuvre de nouveaux plans d’actions. Nous avions également toutes les normes qualités nécessaires et obligatoires pour vendre nos pièces sur nos marchés automobile, aéronautique, etc.
Lorsque nous lui avons expliqué tout cela et montré nos QRQC au Sensei, il n’a fait que lever les yeux au ciel. Mais alors, que voyait-il que nous ne savions pas voir ?
Le JIDOKA
Comment se fait la qualité ?
Le système de production de Toyota (TPS) est très clair là-dessus : il s’agit du JIDOKA. Le JIDOKA est un des deux piliers du TPS, pourtant peu d’ouvrages en détaillent sa pratique contrairement à ceux traitant du flux.
Le concept JIDOKA est apparu lorsque Sakichi TOYODA étudia les métiers à tisser sur lesquels travaillait sa mère pour faciliter le travail de celle-ci. En réalisant des petites innovations les unes après les autres, Sakichi créa les métiers à tisser les plus performants du marché, pouvant s’arrêter tout seul en cas de défaut, ce qui nécessitait moins de surveillance par un opérateur, qui pouvait à la place passer du temps à ajouter de la valeur au produit. Ce concept, Kiichiro TOYODA le pratiquera également lorsqu’il se lancera dans la fabrication d’automobiles. Ce concept du JIDOKA est presque donc l’essence de ce qui fait Toyota, Toyota.
Taiichi Ohno définit le JIDOKA dans son livre Toyota Production System : Beyond Large-Scale Production comme suit :
« Jidoka signifie que l’équipement est immédiatement stoppé lorsqu’un problème survient, de sorte qu’aucun produit défectueux n’est fabriqué. En d’autres termes, il s’agit d’un processus de contrôle de la qualité qui fonctionne indépendamment des machines ou des opérateurs. »
Pour répondre à la définition donnée par Taiichi Ohno, il faut 2 conditions :
· Que la machine (ou le processus) ait vu le problème
· Une connaissance et une maîtrise de la machine (ou du processus ou du produit)
Le JIDOKA signifie d’abord voir le défaut
En effet, pour que la machine (ou le processus) s’arrête de produire lorsqu’elle rencontre un problème, il faut qu’elle détecte qu’il s’agit d’un défaut. Seulement une machine (à injecter par exemple) n’apprend pas. Les personnes, elles, le peuvent.
Pour que les machines fabriquent donc moins de défauts grâce au JIDOKA, il faut que les hommes qui les utilisent et qui les conçoivent apprennent à voir les modes de défaillances.
Dans son live The Toyota Way of Dantotsu Radical Quality Improvement, Sadao Nomura nous décrit dans les premières pages la première clé du secret du niveau de qualité chez Toyota :
Présenté ainsi, cela semble évident. Catégoriser les défauts par rapport à l’endroit où ils ont été détectés ne semble alors pas révolutionnaire.
Mais cette classification a un impact tout différent lorsque nous adoptons délibérément une posture JIDOKA, et l’on comprend mieux l’intérêt de tous les outils qui lui sont liés.
Nous nous concentrons habituellement sur l’occurrence, ou « comment le défaut est apparu ? », Toyota est obsédé par la détection, ou « pourquoi nous n’avons pas vu ce défaut avant ? ». Cela ne veut pas dire qu’ils se fichent de l’occurrence, bien au contraire. Mais leur premier réflexe, issu de la pratique du JIDOKA, est de se demander pourquoi le défaut n’a pas été détecté en amont.
Leur premier point d’attention est de ramener la détection au plus près de l’occurrence du défaut. Leur posture est de se dire qu’un défaut qui a été vu chez le client, ou au process suivant, est un défaut qui « n’a pas été vu » lors de l’opération d’ajout de valeur.
De manière habituelle, on observe dans les usines un « mur qualité » : un contrôle et un tri des pièces par une équipe loin de la production et plus souvent rattachée à la fonction qualité, qui se charge de trouver les pièces défectueuses après production et avant l’envoi au client pour le sécuriser. Cette démarche, certes orientée pour protéger le client a un impact sur la culture de qualité en production. En effet, alors que les opérateurs de production apprennent que leur pièces sont de toutes manières contrôlées par le mur qualité, sans aucun retour sur leur niveau de qualité, ceux-ci se concentrent nécessairement sur produire toujours plus de pièces, souvent pour compenser le pauvre niveau de qualité.
Enfin, les seules données recueillies autour de ces murs qualité sont usuellement les coûts. En 3 ans dans une usine fonctionnant ainsi, je n’ai jamais entendu parler des types de défauts trouvés lors des tris, ni jamais se poser la question : « Pourquoi ce défaut n’a-t-il pas été vu ? » ou « Comment pourrions-nous aider les opérateurs de production de cette pièce à voir ce défaut ? ». Au-delà du coût qu’ils impliquent, la plus grande perte générée par ces murs qualités se trouve donc dans la perte de connaissance et d’apprentissage du personnel de production dans la détection des défauts.
Au contraire, le JIDOKA se concentre à construire une connaissance des modes de défaillances des produits, des machines et des processus par un apprentissage partagé et la pratique délibérée de CHERCHER et VOIR les défauts au plus proche de leur occurrence. C’est en effet ce que faisait le métier à tisser de Sakichi : lorsqu’un fil se cassait, des fines lamelles de métal tombaient et venaient bloquer le métier à tisser et donc arrêter la production. Cet arrêt est avant tout une aide de la machine pour indiquer à l’opérateur à venir voir lui-même le défaut. Et Sakichi a bien dû comprendre où le défaut pouvait bien se produire avant de pouvoir appliquer une contre-mesure.
Nos murs qualité sont pourtant des mines d’or, si tant est qu’on veuille bien s’intéresser aux bonnes valeurs qu’ils recueillent. Classez les défauts par catégories, et posez-vous régulièrement les questions :
Où ce défaut peut-il être détecté en amont dans la chaîne de valeur ?
Comment pouvons-nous aider les opérateurs à voir ce défaut ?
Avant de vous poser la question : comment ce défaut est-il apparu ?
Ce faisant, vous aurez l’opportunité de discuter avec les personnes créant la valeur et pourrez découvrir avec elles comment mieux détecter ce défaut dans les processus qui les ont créés grâce à des aides visuelles comme des poka-yoke, par exemple.
« S’arrêter, c’est gagner du temps … Pas en perdre ! »
Maintenant, il ne suffit pas juste de VOIR les défauts lorsqu’ils se produisent. Nous pouvons très bien voir et ne rien en faire.
Le deuxième secret du JIDOKA réside dans l’arrêt au premier défaut. Comme l’expliquait Taiichi Ohno, l’équipement ou le processus s’arrête au premier défaut afin de ne pas continuer à produire de la non-qualité. Cette notion implique qu’il faille stopper la production et s’intéresser au défaut avant de continuer à produire.
Maintenant que vous apprenez à voir les défauts là où ils se manifestent, il est nécessaire de s’arrêter, observer et comprendre le défaut, discuter avec les gens sur le gemba pour comprendre d’où peut venir ce défaut.
De nouveau, nous voyons dans les usines des machines et processus de production qui déversent leur non-qualité dans des bacs rouges de rebuts, ceux-ci sont souvent posés au sol et maltraités. Pourquoi est-ce qu’on devrait s’y intéresser puisque cela finit à la poubelle ? Seule la valeur compte ! Cela montre au personnel de production que les rebuts et défauts sont une partie intégrante du processus de production, en d’autres termes que la production de pièces de non-qualité est la norme, et nous leur donnons un moyen d’écarter le problème et de passer à la production suivante.
Le BAC ROUGE est l’outil issu du JIDOKA qui permet de s’intéresser à ces rebuts. Prendre chaque jour les pièces se trouvant dans les bacs rouges, continuer à catégoriser les défauts et en les prenant les uns après les autres permet de s’interroger après coup sur ce qui a bien pu se passer dans le processus ou la machine pour produire un tel défaut. Les bacs rouges sont un excellent outil pour :
- continuer à voir de nouveaux défauts et partager l’apprentissage de l’équipe sur la détection ;
- s’interroger sur les conditions qui ont amené ce défaut à se produire. En d’autres termes, refaire l’histoire de la pièce qui l’a malheureusement amenée à se retrouver dans ce bac rouge.
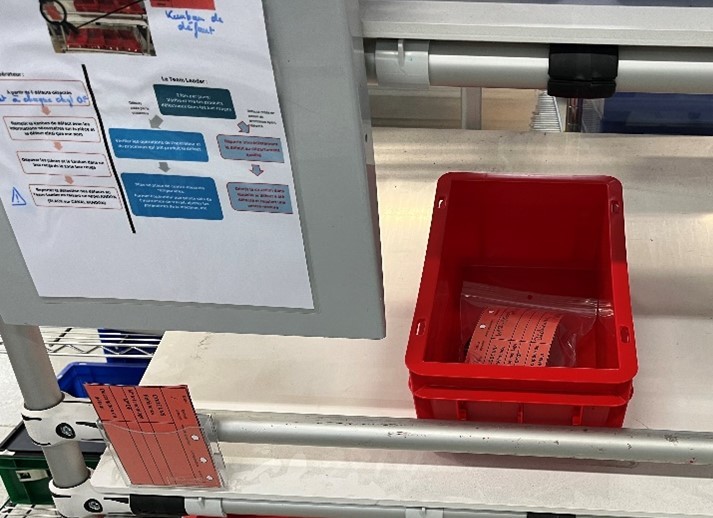
Le deuxième outil clé du JIDOKA pour s’arrêter lorsque l’on rencontre un défaut est l’ANDON. Outil simple dans sa logique, l’opérateur appuie sur un bouton et la ligne s’arrête et le team leader est notifié qu’il y a un problème, et celui-ci peut se rendre sur le poste pour l’aider. Sa mise en place, en revanche nécessite une pratique délibérée et une posture toute particulière aux managers et aux team leaders.
En effet, dans un environnement où les opérateurs sont habitués à simplement mettre de côté les problèmes, ou trouver des solutions par eux-mêmes, prendre, du jour au lendemain, la responsabilité d’arrêter la production semble être un obstacle insurmontable.
Lorsque j’ai essayé moi-même de mettre cela en place sur ma ligne, mes opérateurs m’ont tout de suite affirmé qu’ils avaient compris le principe. Pourtant lors des 5 premiers jours, aucun appel n’avait été fait. Ma première hypothèse fut de penser que c’était parce que l’exigence n’était pas assez haute. Pour corriger cela, j’ai baissé la barre d’appel de 10 rebuts et retouches à 5, mais cela n’a rien changé. Pourquoi donc alors ne recevais-je aucun appel malgré mes véhémences ?
Lors d’une réunion d’équipe un opérateur m’explique :
« Oui ! On a bien compris, lorsqu’on rencontre un problème, si on n’arrive pas à trouver de solution, on fait appel à toi. On ne va pas te déranger à chaque fois qu’on a un problème tout de même ! ».
J’ai été plus que surpris ! Pourtant la cause était simple : nous n’avions pas clarifié ensemble ce qui valait un appel ou non.
C’est donc en étant présent sur le GEMBA, en les accompagnant avec bienveillance que nous avons clarifié et construit ensemble une compréhension commune de ce qui méritait un appel, que le nombre d’appels andon a pu décoller de 0 à 20 du jour au lendemain. Mais ce n’est pas encore fini, une fois que les opérateurs appellent la chaîne hiérarchique, celle-ci doit se transformer en chaîne d’aide, pour lever les doutes, comprendre les défauts ou résoudre le problème qu’ils rencontrent.
Le bac rouge et l’andon ont été, pour moi, deux parfaits cadres pour découvrir 2 secrets de la qualité :
1- Ce sont les gestes des personnes qui font la qualité :
Comme l’a très bien dit l’un de mes opérateurs lors d’une discussion à la suite d’une étude du bac rouge alors que nous parlions du standard de geste pour l’aider à ne pas produire un défaut : « Tous les footballeurs connaissent les bases, mais chacun développe une technique qui lui est propre qui lui permet d’atteindre le même résultat. Aucun ne tape le ballon de la même manière au millimètre près. »
Il m’a fait réaliser que pour produire de la qualité, il ne fallait pas trouver LA seule et unique façon de faire mais bien d’alimenter ce qu’on appelle maintenant sur notre ligne notre « classeur de savoir ». Un playbook de sorte, où sont renseignées toutes nos techniques pour produire. De la base de formation aux techniques plus précises que chaque opérateur aura pu trouver au fil des mois qu’il a passé à produire. Cela leur donne à tous l’opportunité de trouver de nouveaux « plays », de les tester, de les partager dans l’équipe et de former les autres à ces « plays ».
Le rôle du manager n’est pas ici d’imposer une seule façon de faire à tous (comme est souvent l’interprétation des standards) mais de motiver les personnes à découvrir et tester de nouvelles choses, de rassurer ceux qui ne réussissent pas et d’accompagner la formalisation de nouvelles techniques. La chaîne d’aide !
2- La qualité est construite dans le produit et dans son process :
Chaque appel andon est pour le manager un moment privilégié pour voir le produit, le toucher et comprendre ce qui lui arrive lors de notre processus de fabrication. Qu’est-ce qu’on lui fait subir ? Qu’essaye-t-il de nous dire lorsqu’un défaut apparaît ?
Les produits ne m’ont jamais autant parlé depuis que l’andon a été mis en place.
Chaque défaut est une expression du produit qui n’a pas supporter ce que le processus lui a fait. Mais aussi une expression de ce que le produit sait ou ne sait pas faire. Dans mon cas, par exemple, qu’est-ce que la matière sait supporter en termes de chaleur, frottements, exposition, force, dilatation, etc ?
Savoir identifier ces points de défaillance permet par la suite d’améliorer le processus et le produit en y intégrant nos apprentissages. Comme Sakichi Toyoda l’a fait lorsqu’il regardait sa mère travailler sur les métiers à tisser.
Par exemple, cela nous a permis d’identifier que maintenir à une certaine température notre mandrin en PTFE créait une réaction positive de réduction des frottements avec notre pièce en élastomère, ce qui nous permet d’assurer une meilleure qualité du produit tout en réduisant nos efforts à la réaliser. Ou encore affiner les réglages de nos moyens de production en trouvant la parfaite combinaison de température et de circulation d’air pour assurer que nous ne brûlions pas la matière de nos pièces.
« Qu’est-ce que vous faîtes encore là ? »
Qu’essayait donc de nous dire le sensei en nous posant cette question ?
Il avait simplement vu que nous faisions de la qualité classique :
- Déployer les normes ISO et audits certifiants ;
- Positionner des murs qualité lorsque les clients se plaignent ou lorsque nous avons un gros doute sur notre capacité à produire de la qualité ;
- Concentrer nos efforts sur trouver des moyens de contrôler et réduire nos coûts de non-qualité (COPQ) en négociant des sociétés de tri externe moins cher qu’en interne ;
- Mettre en place des bacs rebuts (et non des bacs rouges) sur chacun de nos postes pour permettre à nos opérateurs et machines de ne pas se soucier de la qualité puisque cela allait être jeté ou trié derrière eux ;
- Imposer des standards uniques à tous, les contrôler par des checklists et des audits de poste puis réprimander les dysfonctionnements par des plans d’action se soldant par des retours aux standards à la suite de résolutions de problèmes où la cause « manque de rigueur » est la plus présente.
Il nous poussait à voir qu’améliorer la qualité passait d’abord par :
1- S’intéresser vraiment aux défauts en allant les voir.
Ne parlez plus de rebuts, mais de défauts. Et arrêtez de demander les coûts de tri, demandez plutôt les catégories des défauts.
Identifiez de quel processus de fabrication ils peuvent provenir. Que pouvons-nous faire pour les détecter au plus près de là où ils sont créés ? Qu’est-ce que les opérateurs de production connaissent de ces défauts et comment les motiver à s’y intéresser ?
C’est ce que Nomura-sensei appelle dans ses programmes DANTOTSU le Weak Point Management (WPM).
Aidez vos collaborateurs à reconnaître les défauts grâce aux poka-yoka, aux défauthèques, aux « champs de chou » ou potagers et aux bacs rouges. Et donnez-leur le pouvoir de stopper la production grâce à l’andon. Surtout ne paniquez pas si vos processus détectent désormais plus de défauts ! Mais observez ce qui se passe au niveau de vos murs qualité et auprès de vos clients (internes et même externes).
2- Pour s’intéresser et comprendre profondément la façon dont nous produisons et concevons nos processus et nos produits.
Chaque défaut détecté vous permet de questionner le processus et le produit. De comprendre leurs points de défaillance respectifs et réfléchir en équipe aux manières de concevoir toujours plus de qualité intégrée dans vos produits et processus, à l’instar des nombreuses itérations kaizen qui ont mené la maison Toyoda jusqu’au model G.
S’améliorer durablement pour produire des produits de qualité commence donc par l’intérêt authentique que l’on souhaite porter aux défauts et à comprendre ceux-ci. Ce qui nous a fait louper ces défauts, ce que nous aurions pu faire pour ne pas créer le défaut et ce que nous pouvons faire différemment pour continuer à produire une plus haute qualité avec des futurs produits et processus intégrant toujours plus de systèmes indépendants permettant de contrôler la qualité.
Le sensei nous invitait donc à initier de nous-même une pratique personnelle des préceptes du JIDOKA en apprenant à voir par la façon dont nous traitions dans tous les niveaux de notre organisation nos produits défectueux et les processus qui les ont créés.
Et vous ? Comment vous occupez-vous de vos défauts ?
Marc-Antoine Guichard
Abonnez-vous à Articles ILF sur Linkedin
Pour connaître et exercer vos droits, notamment de retrait de votre consentement à l'utilisation des données collectées par ce formulaire, veuillez consulter notre politique de confidentialité.